Due to the environmental emergency linked to plastic, manufacturers find themselves committed to developing post-consumer plastic recycling processes. In addition to traditional mechanical recycling, the SABIC Group has perfected the post-consumer plastic packs conversion into polyolefin.
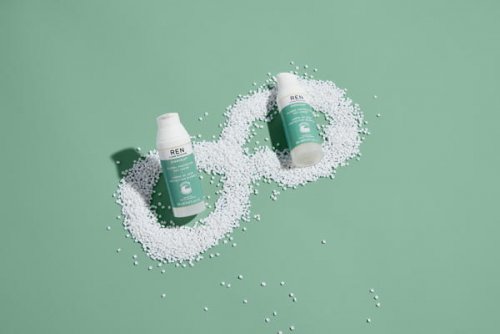
"The plastic challenge has shed light on the need to provide additional solutions. It has made possible to unlock and deepen a whole series of technological innovations, in particular the novel application of pyrolysis for this new recycling technology proposed by SABIC," notes Frédéric Dreux. "But beware, these techniques do not free yourself from improving eco-design, key to achieve mono-material packs, these efforts remain a priority and an absolute necessity. These new technologies are also not meant to replace mechanical recycling. It is a necessary addition to further increase recycling capacities," he adds.
Besides reducing the carbon impact compared to virgin plastics of fossil origin, the advantage of this technology lies in the possibility to focus on the recycling of packs which are known to be more difficult to recycle using a mechanical process, and which are therefore commonly sent to incineration or landfill. "These are often packagings that do not fit into the ’guidelines’ of what recyclers are able to process, such as flexible pouches or complex multi-material products. High quality mechanical recycling requires huge sorting efforts upstream, because once re-melted into pellets, it will be impossible to separate the materials. Here, we are talking about molecular fragmentation, which means the technology is less sensitive to the mix of PP + PE materials in the same batch. Traces of PET, or even of metal in the event of metallization, are no longer an issue for this technology" explains the specialist. A sore point for the luxury and cosmetic industry, which has to deal with complex materials to answer the need for barrier properties or complex assemblies for functionality.
Similar to a virgin material
The technology reverts to the basic constituent of plastic with the same qualities, properties, clarity and purity than the virgin material. "Going to the molecular level allows recreating all of the polyolefin grades and to serve applications in the finest and most optimum way. For the first time, we have a recycling technique, opening the possibility of indefinite plastic recycling without losing its quality and physical properties," specifies Frédéric Dreux.
"It is important to support new recycling technologies, and this is what we are doing with REN Clean Skincare, even if it now represents a cost for the brand, a cost, we decided consumers should not have to bear. Our support to this technology can help make it grow to an industrial scale, with an increase in new capacities and structures. This is not going to be achieved by a supplier alone, the good news is that there is a real consensus from the sector to increase resources for this new technology. It’s a virtuous circle. This is a new step in the way to improve the sustainability of plastics, demonstrating that it is possible to develop and use new technologies to further contribute to plastic being recycled in a circular economy" concludes Frédéric Dreux.